Exploring the Benefits and Applications of Silicone Membranes for Vacuum Presses
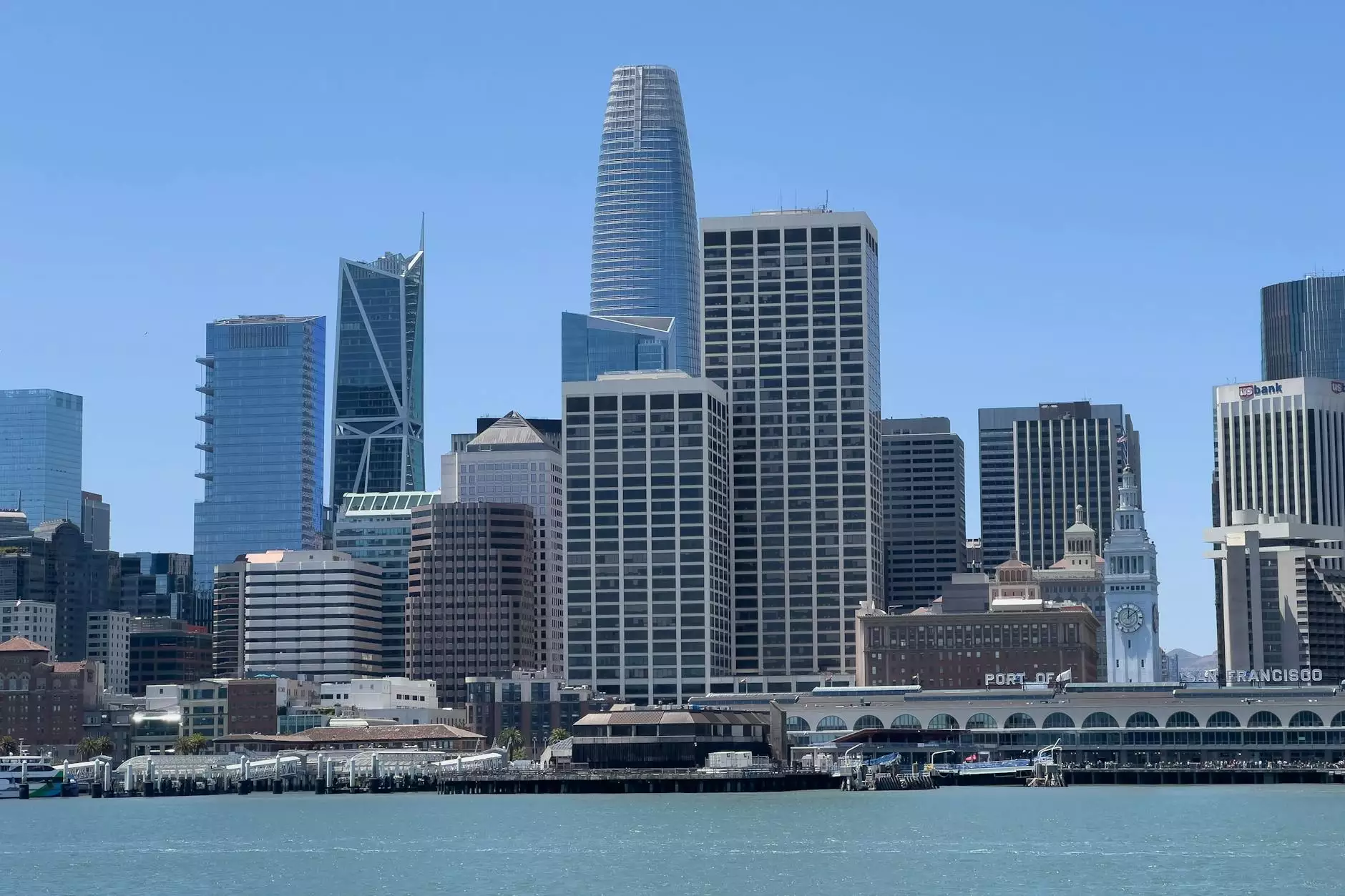
In today's rapidly evolving industrial landscape, silicone membranes for vacuum presses have emerged as a vital component in various manufacturing processes. These membranes offer remarkable versatility and efficiency, making them essential in sectors such as woodworking, composite materials, and more. This article delves deep into what silicone membranes are, their advantages, and their unique applications in vacuum pressing.
What is a Silicone Membrane?
A silicone membrane is a flexible, durable sheet made from high-quality silicone rubber. These membranes are designed to create an airtight seal, enabling effective vacuum sealing in various applications. Their unique properties make them suitable for use in environments that require precision and reliability.
Why Choose Silicone Over Other Materials?
Silicone membranes present numerous advantages compared to traditional rubber or plastic materials. Some of these benefits include:
- Heat Resistance: Silicone membranes can withstand higher temperatures without losing their structural integrity, making them ideal for applications that involve heat.
- Flexibility and Durability: The elastic properties of silicone allow for repeated stretching and bending, which enhances their lifespan.
- Chemical Resistance: Silicone is resistant to many chemicals, making it suitable for a variety of industrial settings.
- Non-Stick Surface: The non-porous nature of silicone prevents material adhesion, leading to cleaner production processes.
Applications of Silicone Membranes in Vacuum Pressing
Silicone membranes are extensively used in vacuum pressing across multiple industries. Here are some specific applications:
1. Woodworking and Laminating
In woodworking, silicone membranes enable efficient lamination processes. The vacuum press, combined with silicone membranes, ensures that veneers, laminates, and hardwoods are bonded seamlessly. This technique enhances product quality by eliminating air bubbles and ensuring a perfect mold.
2. Composite Material Manufacturing
Silicone membranes are also critical in the manufacture of composite materials. In this context, they are used to form complex shapes and ensure uniform pressure distribution during the curing phase. This results in a stronger final product, which is essential in aerospace and automotive industries.
3. Medical and Laboratory Applications
In the medical field, the precision of silicone membranes for vacuum applications is invaluable. They are used in the production of various medical devices where cleanliness and sterilization are paramount. Additionally, laboratories utilize silicone membranes to maintain vacuum conditions for experiments and sample preservation.
4. Graphic Arts and Printing
The graphic arts industry benefits from silicone membranes in the manufacturing of high-quality prints. They are used in the printing process to achieve an excellent finish, ensuring that colors are vibrant and materials are securely adhered.
The Advantages of Using Silicone Membranes in Vacuum Pressing
The use of silicone membranes for vacuum presses offers an array of benefits that can significantly enhance manufacturing processes. Here are some key points:
- Cost-Effectiveness: Although the initial investment in silicone membranes might be higher, their durability and longevity make them a cost-effective solution in the long run.
- Improved Product Quality: The ability to create a tight seal ensures that products are free from defects associated with air pockets or inconsistent pressure.
- Easy Maintenance: Silicone membranes require minimal maintenance compared to other materials, saving time and increasing productivity.
- Environmental Benefits: Many silicone membranes are manufactured with eco-friendly processes and are fully recyclable, thereby supporting sustainable manufacturing practices.
How to Choose the Right Silicone Membrane for Your Vacuum Press
Selecting the appropriate silicone membrane involves considering several factors to ensure optimal performance in your specific application:
1. Thickness
The thickness of the membrane is crucial. Thicker membranes may offer more durability, while thinner membranes could provide better flexibility. Assess the requirements of your application to decide.
2. Temperature Resistance
Depending on the heating requirements of your vacuum press, choose a silicone membrane that can withstand the necessary temperatures without degrading.
3. Chemical Compatibility
Evaluate the types of materials you will be using with the membrane. Ensure that the silicone is compatible with the chemicals involved in your process.
4. Size and Dimensions
Consider the size of your vacuum press and the dimensions required for effective operation. Custom sizes may be necessary for specific configurations.
5. Supplier Reputation
Opt for a supplier with a strong reputation and positive reviews in the industry. The quality of the silicone membrane can significantly affect the longevity and efficiency of your vacuum press.
Where to Purchase Silicone Membranes for Vacuum Presses
For businesses looking to invest in silicone membranes for vacuum presses, visiting established suppliers is essential. A leading choice in the market is silicone-membranes.eu, where a wide range of membranes are available for sale. Their offerings include:
- Standard Silicone Membranes: Available in various sizes and thicknesses.
- Custom Silicone Solutions: Tailored membranes to meet specific industrial needs.
- Technical Support: Expert guidance on selecting and using silicone membranes effectively.
Conclusion
The increasing demand for high-performance materials in industrial applications has highlighted the significance of silicone membranes for vacuum presses. Their unique properties, combined with their versatility and durability, make them indispensable in a multitude of sectors. When selecting a silicone membrane, consider factors such as thickness, temperature resistance, and supplier quality to ensure the best outcomes for your business. As industries continue to evolve, silicone membranes will undoubtedly remain at the forefront of innovative manufacturing processes.
silicone membrane for vacuum press