CNC Precision Machining Manufacturers: The Backbone of Modern Industry
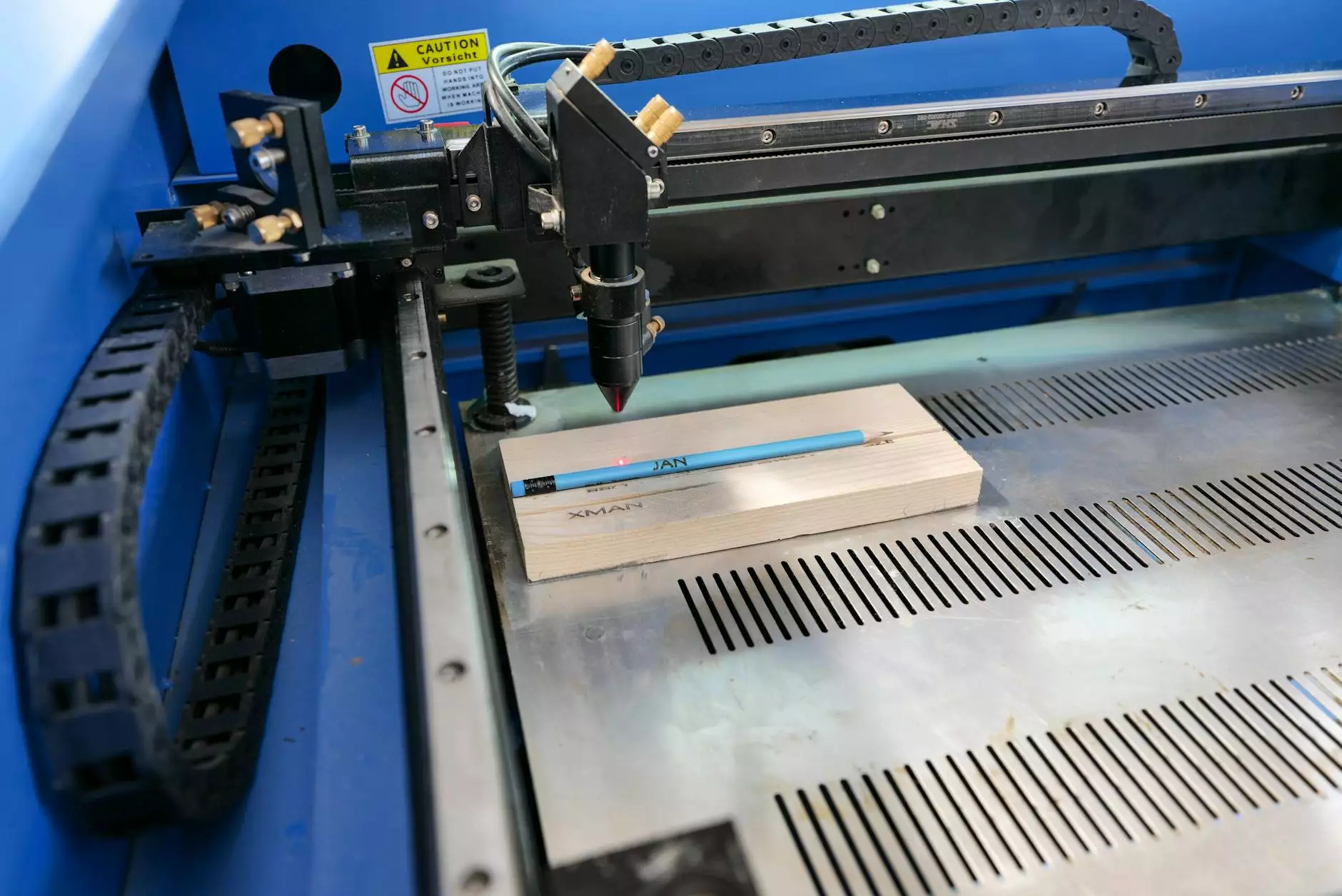
The realm of cnc precision machining manufacturers is a vibrant and ever-evolving segment of the manufacturing industry. CNC machining, which stands for Computer Numerical Control, is a pivotal method utilized for creating precise and intricate parts across various sectors including aerospace, automotive, and medical equipment. In this article, we will dive deep into the fundamentals, advantages, and future trends of CNC precision machining, particularly focusing on the prominent role played by manufacturers in this field.
Understanding CNC Precision Machining
CNC precision machining is a method that uses computer-controlled machines to manufacture components with high accuracy. The process involves the removal of material from a workpiece—often metal or plastic—using various subtractive manufacturing techniques. This approach allows for remarkable precision and reproducibility, making it an essential technique in modern manufacturing.
Types of CNC Machining Processes
- Milling: A process that uses rotating cutters to remove material from a workpiece. This is ideal for creating complex shapes.
- Turning: Involves rotating the workpiece while a tool is applied to cut the material. This is commonly used for cylindrical parts.
- Electrical Discharge Machining (EDM): A technique that uses electrical discharges to remove material, particularly useful for hard metals.
- Laser Cutting: Uses focused laser beams to cut materials, known for its precision and versatility.
- 3D Printing: While distinct, advanced CNC techniques are increasingly integrated with additive manufacturing for component creation.
The Role of CNC Precision Machining Manufacturers
CNC precision machining manufacturers play a critical role in the supply chain of various industries. They are responsible for producing parts that meet exacting standards and specifications. Here are the essential functions they serve:
1. Quality Assurance
Quality control is paramount in CNC machining. Manufacturers invest heavily in advanced inspection technology to ensure that each part is produced to exact specifications. They follow rigorous protocols to enforce tolerances and validate the integrity of materials used.
2. Customization
Today's manufacturers are not just part makers; they are solution providers. They offer tailored machining services to meet specific client requirements, enabling businesses to innovate and stay competitive.
3. Efficiency and Cost Effectiveness
With the aid of sophisticated CNC machinery, manufacturers can produce parts in large volumes while maintaining efficiency. This maximizes cost effectiveness and reduces lead times, key components in today's fast-paced market.
4. Expertise and Collaboration
These manufacturers employ skilled engineers and technicians who are well-trained in the latest CNC technologies. Their expertise allows for collaborative efforts with clients, ensuring that the final product truly meets the client's vision and engineering needs.
Benefits of CNC Precision Machining
The advantages of engaging with CNC precision machining manufacturers are numerous:
- High Precision and Accuracy: CNC machines can achieve tolerances within fractions of a millimeter, making them essential for industries that require high precision.
- Complex Geometries: The ability to produce complex shapes that would be impossible with traditional manufacturing methods is a significant advantage.
- Reduction in Waste: CNC machining is a subtractive manufacturing process, which means it only uses the material necessary for the part, leading to less material wastage.
- Scalability: Whether producing a single prototype or thousands of parts, CNC machining can easily scale operations to meet demand.
- Enhanced Flexibility: Quick adjustments can be made in the programming, allowing manufacturers to respond swiftly to changing orders or designs.
Industries That Benefit from CNC Precision Machining
Numerous industries rely on CNC precision machining manufacturers to meet their production needs:
- Aerospace: Requires parts that comply with strict safety and performance standards.
- Automotive: Uses precision parts for engine components, gear systems, and other crucial parts.
- Medical Devices: Demands flawless precision for instruments and implants that are critical to patient safety.
- Electronics: Needs precision components for circuit boards and enclosures.
- Industrial Machinery: Relies on custom parts for manufacturing equipment and tools.
The Future of CNC Precision Machining
As technology progresses, so does the field of CNC precision machining. Here are some future trends to watch for:
1. Automation and Industry 4.0
The incorporation of IoT (Internet of Things) in machining technologies allows machine tools to communicate with each other, enhancing productivity through automation. Manufacturers are increasingly adopting smart factories that leverage data to optimize operations.
2. Advanced Materials
With the continuous development of new materials, CNC manufacturers are adapting to machined composites and high-performance alloys, which will open new applications and possibilities.
3. Green Machining
Environmental considerations have led to the adoption of sustainable practices in machining. Manufacturers are exploring methods to reduce energy consumption and utilize environmentally friendly materials.
4. Integration with Additive Manufacturing
The combination of CNC machining with additive processes is changing the landscape, allowing for hybrid manufacturing systems that can produce parts faster while maintaining high precision.
Choosing the Right CNC Precision Machining Manufacturer
Selecting a suitable manufacturer is crucial to the success of your project. Here are some tips for choosing wisely:
1. Check Their Experience and Expertise
Invest time in researching the manufacturer's background. A company with extensive experience in your industry will have a better understanding of specific challenges and requirements.
2. Assess Their Technology and Machinery
Cutting-edge technology can directly affect the quality of the parts produced. Ensure the manufacturer utilizes modern CNC machines that can accommodate your project's needs.
3. Review Their Quality Control Processes
Inquire about the manufacturer's quality assurance measures. Effective quality control will ensure that your components meet the required standards and specifications.
4. Look for Positive Customer Reviews
Feedback from previous clients can provide valuable insight into the reliability, quality, and service of the manufacturer.
Conclusion
In conclusion, the landscape of cnc precision machining manufacturers is integral to the advancement of modern manufacturing across various industries. Their ability to deliver high-quality, precise components not only fuels countless applications but also drives technological innovation. As we look to the future, trends such as automation, advanced materials, and the integration of additive manufacturing will continue to enhance the capabilities of these manufacturers. By understanding the complexities and opportunities within this industry, businesses can make informed decisions that propel their success in an increasingly competitive market.
For organizations in need of superior CNC precision machining solutions, partnering with a reputable manufacturer like DeepMould.net can provide the competitive edge necessary for achieving operational excellence.