Electric Plastic Molding: Transforming the Business Landscape
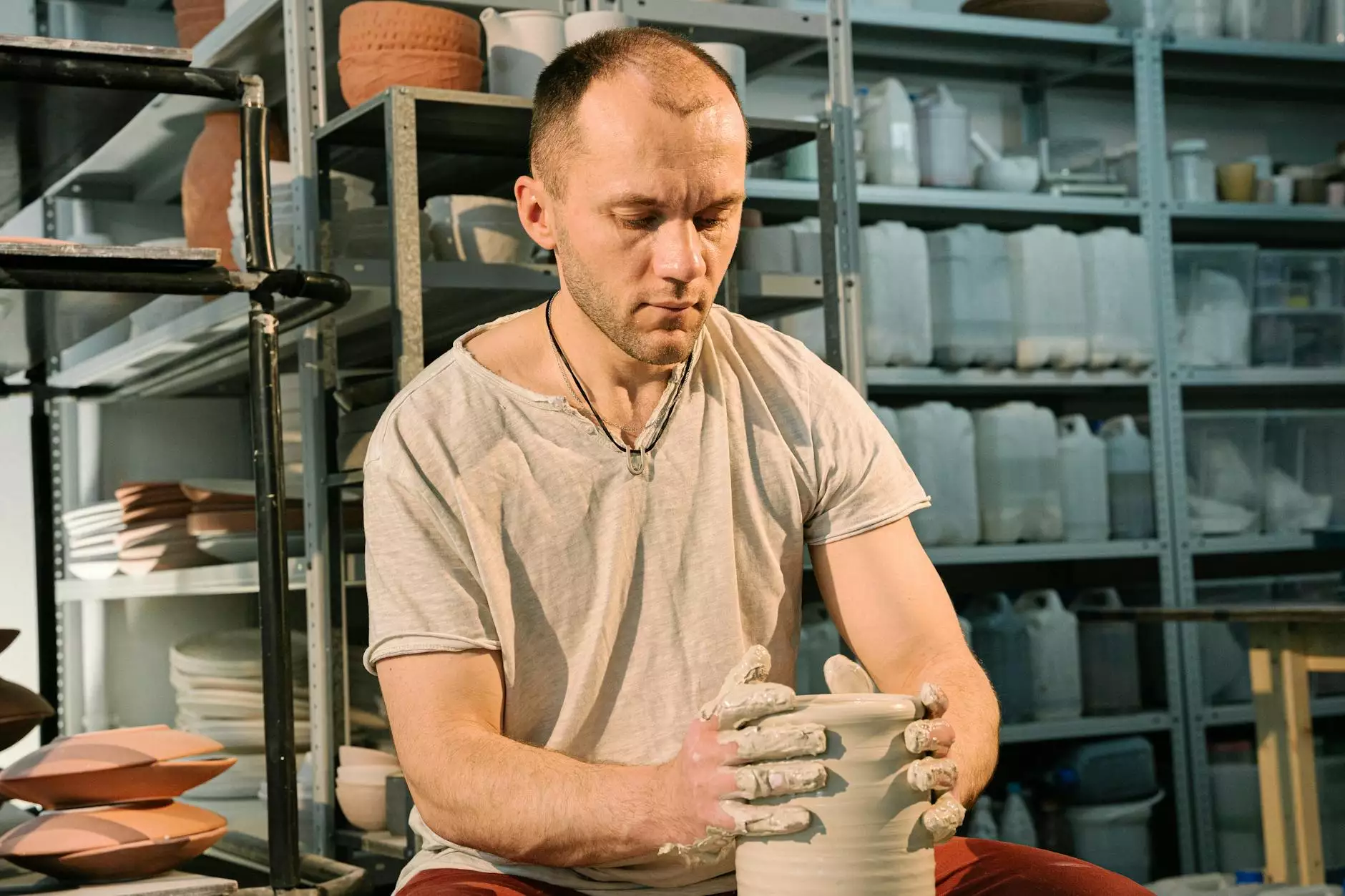
Introduction to Electric Plastic Molding
In today's fast-paced manufacturing environment, the need for efficiency and sustainability has never been greater. Among the various technologies ensuring these goals is Electric Plastic Molding. This innovative method not only enhances the precision and speed of production but also aligns with the market's increasing demand for eco-friendly solutions. In this article, we will delve into the intricacies of Electric Plastic Molding, its benefits, applications, and its undeniable impact on the business landscape.
The Process of Electric Plastic Molding
Electric Plastic Molding is a process where electrical energy is used to drive the injection molding process. Unlike traditional hydraulic molding, which relies on hydraulic fluid and pumps, electric molding machines use electric servos to execute the molding cycle. This method brings forth numerous advantages:
- Precision and Control: The use of electric drives allows for exceptional precision in the molding process, resulting in better quality products.
- Energy Efficiency: Electric machines consume less power compared to hydraulic machines, making them a more sustainable choice.
- Reduced Cycle Time: The speed of electric machines can significantly reduce production times, leading to increased output.
- Low Maintenance Costs: With fewer moving parts compared to hydraulic systems, electric molding machines generally require less maintenance.
Applications of Electric Plastic Molding
Electric Plastic Molding is used in various industries, showcasing its versatility and efficiency. Common applications include:
- Automotive Industry: Electric molding is ideal for producing components like gears, clips, and knobs where precision is crucial.
- Electronics: Components such as casings, connectors, and intricate parts benefit greatly from the precision offered by electric molding.
- Medical Devices: The need for sterile, precise, and reliable medical components makes electric molding an attractive option in this sector.
- Toys and Consumer Goods: The ability to produce complex designs with safety standards in mind makes this technology prevalent here.
Benefits of Electric Plastic Molding
Understanding the benefits offered by Electric Plastic Molding is crucial for businesses looking to invest in this technology. Here are some key advantages:
1. Enhanced Production Efficiency
Electric Plastic Molding drastically improves production efficiency by:
- Reducing cycle times by up to 30%.
- Minimizing energy consumption due to optimized processes.
- Allowing for faster setup and changeover times.
2. Superior Product Quality
With precision control, Electric Plastic Molding enhances product quality through:
- Consistent cycle times ensuring uniform output.
- Improved dimensional accuracy, crucial for high-end products.
- Better surface finishes due to lower melt temperatures.
3. Environmental Impact
The shift towards sustainable manufacturing practices is essential for modern businesses. Electric Plastic Molding contributes positively by:
- Reducing energy usage by up to 60% compared to traditional methods.
- Minimizing waste through precise material usage and control.
- Lower emissions, aligning with global sustainability goals.
Electric Plastic Molding vs. Hydraulic Molding
When comparing Electric Plastic Molding with traditional hydraulic systems, several differences stand out:
1. Energy Consumption
As mentioned, electric machines use significantly less energy, contributing to reducing operating costs.
2. Maintenance and Downtime
Electric machines have fewer parts to maintain, leading to lesser breakdowns and increased uptime in production. Hydraulic systems often face issues with leaks and fluid replacement, impacting overall productivity.
3. Precision and Dynamic Control
The precise control provided in electric molding systems allows for quicker adjustments and more intricate designs. In contrast, hydraulic systems may struggle to manage complex geometries.
Future Trends in Electric Plastic Molding
As technology evolves, so does Electric Plastic Molding. Businesses should keep an eye on these emerging trends:
1. Integration of Automation and AI
Modern electric molding machines are becoming increasingly integrated with automated processes and artificial intelligence. This development will enhance precision, predict maintenance needs, and optimize production schedules.
2. Development of Biodegradable Materials
The ongoing demand for eco-friendly materials drives the development of biodegradable plastics that can be used in electric molding, further reducing the environmental impact of manufacturing.
3. Increased Customization
As customer demands for personalized products grow, electric molding technology will likely advance to facilitate even greater customization options in product design.
Conclusion
In conclusion, Electric Plastic Molding stands as a transformative force in the manufacturing industry. Its advantages in efficiency, precision, and environmental sustainability make it a compelling choice for businesses looking to innovate and meet the demands of the modern market. By embracing this technology, companies can not only enhance their production capabilities but also contribute positively to the world around them.
To gain a competitive edge, explore the vast opportunities Electric Plastic Molding presents. Businesses like Deep Mould are leading the way in this revolution, utilizing advanced technologies to produce high-quality molded products that comply with industry standards.