Understanding Mold Tooling: The Backbone of Precision Manufacturing
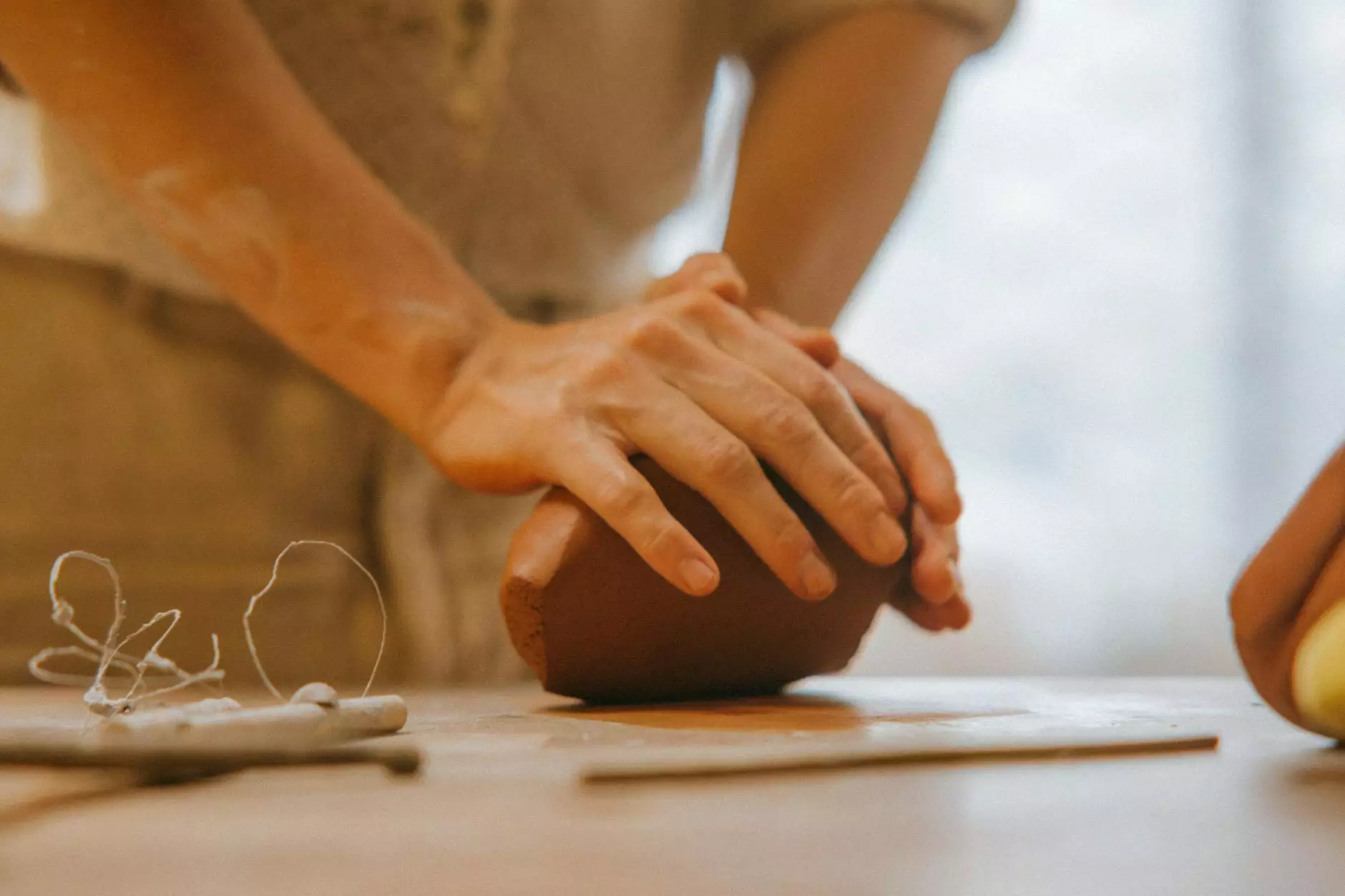
In the dynamic world of manufacturing, mold tooling plays a critical role in ensuring product accuracy, efficiency, and quality. This article delves into the intricacies of mold tooling, its types, benefits, and its relationship with metal fabricators. Understanding mold tooling is essential for businesses looking to optimize their production processes and maintain a competitive edge in their industries.
The Essentials of Mold Tooling
Mold tooling refers to the process of designing and creating molds that are used to shape materials into desired forms. This process is integral to various manufacturing industries, especially in the production of complex shapes and components. The process involves several steps, including:
- Designing the Mold: The first step in mold tooling involves designing the mold based on the specifications of the product. Advanced CAD (Computer-Aided Design) software is typically used to create precise and detailed designs.
- Fabrication of the Mold: Once the design is finalized, the mold is fabricated using materials such as steel or aluminum, ensuring durability and precision.
- Testing the Mold: After fabrication, the mold is subjected to rigorous testing to ensure it meets the required specifications and functions correctly.
- Production: Once the mold passes testing, it can be used in production, allowing for the mass creation of uniform parts.
Types of Mold Tooling
There are various types of mold tooling used in manufacturing, each suited for different applications. Understanding these types can help businesses make informed decisions about which tooling method to adopt.
1. Injection Molding
Injection molding is perhaps the most common form of mold tooling. It involves injecting molten material into a mold cavity where it cools and solidifies into the desired shape. This method is ideal for mass production and offers high precision. Key advantages include:
- High production speed
- Consistent product quality
- Ability to produce complex shapes
2. Blow Molding
Blow molding is similar to injection molding but is specifically used for creating hollow parts such as bottles and containers. This technique involves blowing air into a molten tube, which expands to form the shape of the mold. The benefits of blow molding include:
- Efficient production of hollow shapes
- Low material waste
- Versatility in design
3. Compression Molding
Used mainly for thermoplastic and thermosetting materials, compression molding involves placing a pre-measured amount of material into a heated mold cavity. The mold is then closed, and pressure is applied until the material cures. This method is efficient for producing larger parts and has advantages such as:
- Lower tooling costs
- Ability to work with bulky materials
- Good surface finish results
4. Rotational Molding
Rotational molding is ideal for creating large, hollow parts. It involves rotating a mold to evenly distribute the molten material across its surface. This method is particularly effective for creating complex shapes and products with uniform wall thickness. Benefits include:
- Low production costs for large parts
- Minimal waste of raw materials
- High versatility in design
The Benefits of Investing in Quality Mold Tooling
Investing in high-quality mold tooling can significantly impact a business's efficiency and profitability. Here are some of the key benefits:
1. Enhanced Product Quality
With precision in design and fabrication, quality mold tooling ensures that products are manufactured to high standards. This results in fewer defects, lower rework costs, and increased customer satisfaction.
2. Increased Production Efficiency
Quality molds reduce cycle times and improve the speed of production. Faster processes lead to higher output rates, allowing businesses to meet market demand more effectively.
3. Cost-Effectiveness
By using precise mold tooling methods, businesses can reduce material waste and optimize resource utilization. Although initial investments may be higher, the long-term savings can be substantial due to fewer defects and improved production timelines.
4. Improved Flexibility and Scalability
Companies that invest in adaptable mold tooling processes can easily modify their production to accommodate changing product lines or market demands, making it easier to stay competitive in a rapidly evolving industry.
Choosing the Right Mold Tooling Partner
For organizations in the manufacturing sector, selecting the right mold tooling partner is crucial. Here are several considerations when making this decision:
1. Experience and Expertise
Look for companies that possess extensive experience in mold tooling and a strong track record in your specific industry. Knowledge and expertise are key indicators of their capability to meet your requirements.
2. Advanced Technology
Choose a partner who utilizes state-of-the-art technology and equipment for mold design and fabrication. Companies that invest in modern machinery are often more capable of producing high-quality products efficiently.
3. Customization Options
A potential mold tooling partner should provide tailored solutions to suit your specific needs, including the ability to create custom molds based on unique specifications.
4. Customer Support
Efficient customer service and support are vital. A responsive partner can address any issues that arise during the production process and provide assistance when needed.
Sustainability in Mold Tooling
Sustainability is becoming a significant concern within the manufacturing sector. Efficient mold tooling practices can contribute to environmentally friendly production processes. Here are ways businesses can implement sustainable practices:
1. Material Efficiency
Using recycled or sustainably sourced materials in mold tooling can significantly reduce the environmental impact. Additionally, optimizing mold design to minimize waste can enhance sustainability.
2. Energy Efficiency
Implementing energy-efficient machinery and processes can greatly reduce the carbon footprint of mold tooling operations. Look for partners that prioritize energy conservation.
3. Lifecycle Analysis
Conducting lifecycle assessments of molds and products helps businesses understand and reduce their environmental impact throughout the manufacturing process.
Conclusion
Comprehending the significance of mold tooling in manufacturing is essential for any business seeking to thrive in today’s competitive landscape. With a focus on quality, efficiency, and sustainability, organizations can enhance their production capabilities, resulting in improved product quality and customer satisfaction. By partnering with seasoned metal fabricators and investing wisely in mold tooling technologies, businesses can position themselves for success and adaptability in the ever-evolving marketplace.
For businesses like deepmould.net, understanding the complexities of mold tooling and making informed choices is pivotal for driving growth and achieving manufacturing excellence.