The Importance of Pressure Vessel Inspection
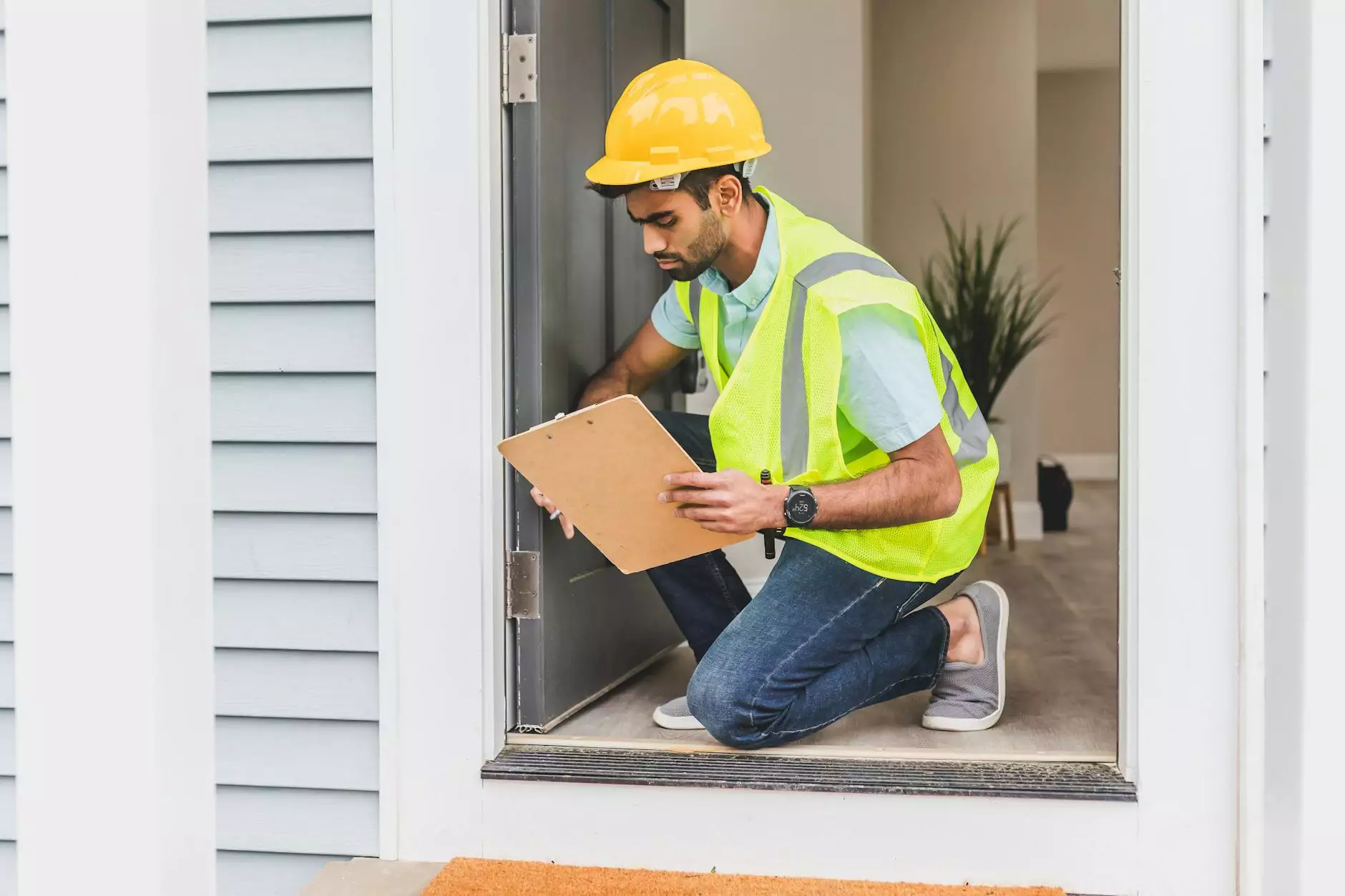
In numerous industries, especially in manufacturing and energy production, pressure vessels play a vital role. They are designed to hold gases or liquids at a pressure substantially different from the ambient pressure. To ensure they operate safely and effectively, thorough and regular pressure vessel inspection is critical. Not only does this inspection safeguard employees and the environment, but it also aligns with regulatory requirements.
What Are Pressure Vessels?
A pressure vessel is defined as a container designed to hold gases or liquids at high pressures. These vessels are typically made from high-strength materials such as steel or composite materials to withstand the intense pressures within. Common examples include:
- Boilers
- Storage tanks
- Heat exchangers
- Gas cylinders
Each type of pressure vessel has specific applications and is subject to various standards and codes to ensure they are manufactured and maintained properly.
The Need for Pressure Vessel Inspection
Regular pressure vessel inspection is essential for several reasons:
- Safety: The primary objective is to ensure the safety of personnel working in environments where pressure vessels are present.
- Regulatory Compliance: Many governments mandate inspections to comply with local and international safety standards.
- Operational Efficiency: Maintaining vessels in optimal condition helps avoid unnecessary downtime and expensive repairs.
- Environmental Protection: Preventing leaks or failures helps in safeguarding the environment from hazardous materials.
Inspection Procedures and Techniques
The pressure vessel inspection process involves several techniques and methodologies designed to detect potential issues before they lead to catastrophic failures. Some of the most common inspection methods include:
Visual Inspection
This is the most fundamental form of inspection, where trained personnel visually assess the condition of the vessel. Key aspects to check include:
- Corrosion
- Cracks
- Weld integrity
- Deformations
Ultrasonic Testing (UT)
Ultrasonic testing is a non-destructive testing (NDT) method that uses high-frequency sound waves to detect imperfections and measure wall thickness. This technique can detect flaws internal to the material that are not visible through visual inspection alone.
Magnetic Particle Testing (MPT)
This method is used primarily for ferromagnetic materials and involves applying magnetic particles to the surface of the vessel. If there are cracks or defects, the magnetic field will be disrupted, allowing for the detection of issues.
Dye Penetrant Testing (DPT)
Dye penetrant testing involves applying a liquid dye to the surface of the vessel. After a specified time, the excess dye is removed, and a developer is applied. Defects will show as colored indications where the dye penetrated.
Radiography
Radiographic testing involves using X-rays or gamma rays to view the internal structure of the vessel. This method is particularly useful for detecting internal flaws such as weld defects and corrosion.
Documentation and Reporting
Every inspection should be thoroughly documented. Accurate records not only assist in compliance with regulatory requirements but also provide invaluable information for future inspections and maintenance planning. Documentation typically includes:
- Inspection findings
- Photographic evidence
- Recommendations for repairs or maintenance
- Historical data for trend analysis
Regulatory Standards and Compliance
Various regulatory bodies establish standards that govern the inspection and maintenance of pressure vessels. In the UK, the Pressure Systems Safety Regulations (PSSR) 2000 provides guidelines that must be adhered to, ensuring that pressure systems are designed, manufactured, and maintained correctly.
It is crucial for businesses involved with pressure vessels to ensure that they are compliant with these regulations to avoid penalties and ensure the safety of their operations. Regular audits and reviews of inspection records can help maintain compliance.
Choosing a Certified Inspection Company
When selecting a company for pressure vessel inspection, it is vital to choose a certified and reputable provider. Look for companies that have experience in your specific industry and employ qualified inspectors who can provide a comprehensive service. Here’s what to consider:
- Certification and accreditation
- Experience with similar pressure vessels
- Client testimonials and case studies
- Service offerings (including emergency inspections)
Conclusion: Prioritizing Safety Through Regular Inspection
In conclusion, the importance of regular pressure vessel inspection cannot be overstated. This process is crucial for maintaining safety, ensuring compliance, and protecting the environment. By implementing a rigorous inspection regime and choosing a qualified inspection service, businesses can mitigate risks and enhance operational efficiency. Always remember, investing in quality inspections is not just about regulatory compliance; it’s about safeguarding human lives and protecting your investment in pressure vessel technology.
For more detailed information and expert support regarding pressure vessel inspection, visit Safe Plant UK, where you can find professional services tailored for your specific needs.